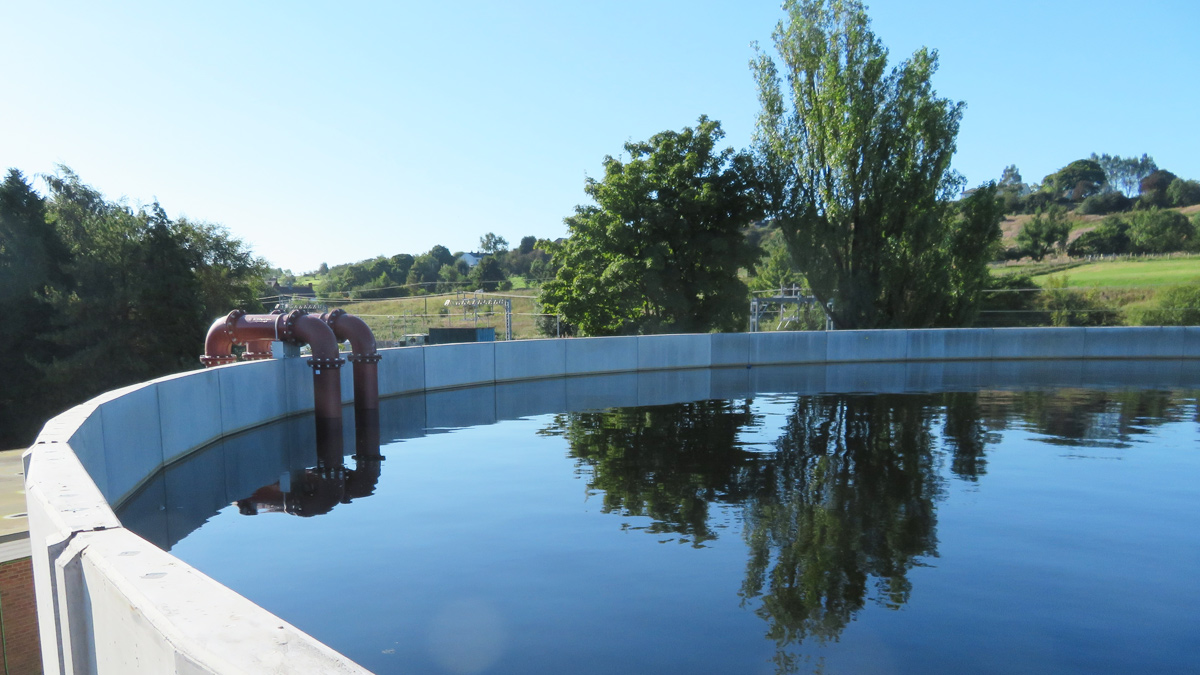
Construction of an above-ground AQUA-TANK® system to enhance the wastewater treatment works’ stormwater detention capacity.
Advance-plus, a joint venture between MWH Treatment, J Murphy & Sons and Stantec UK, are currently delivering a project at Horwich WwTW on behalf of United Utilities. The project is required to deliver the Environment Agency’s Water Industry National Environment Programme (WINEP) and takes into consideration future population growth based on a 2035 design horizon. The requirements for the project are to achieve a final effluent quality of 0.25 mg/l of total phosphorus on an annual average basis and a final effluent quality of 2.5 mg/l iron on a 95%-Ile basis and 8 mg/l iron on a upper tier limit basis. The work will ensure the local River Douglas will achieve a good status under the Water framework directive.
Storm detention tank design development
As part of the solution, a 4600m3 storm detention tank was required to increase capacity on the treatment works. Initially this was proposed to be constructed below ground in an area of site with unfavourable ground conditions where there was a high risk of coal mine workings and excessive Japanese knotweed and Himalayan balsam. This location also included significant lengths of process pipework and pumping to tie it into the existing network. A value engineered alternative solution was proposed in a different location on site. This was developed to be an above-ground solution, using precast concrete panels from A-Consult Ltd on piled foundations.
Enabling works
Early investigation works identified several chartered and unchartered underground services and a critical telemetry cable, all of which had to be diverted or proven redundant prior to piling. Also, several redundant structures were located and broken out. A piling platform was designed by J Murphy & Sons’ temporary works design team and constructed using recycled aggregate.
Piling was completed using J Murphy & Sons’ internal piling capability, JM Piling, that installed 101 (No.) 450mm diameter CFA piles to an average depth of 11.5m. Advance-plus self-delivery workforce then excavated to formation, cropped piles and blinded the tank prior to A-Consult Ltd starting on site. A DN700 pipe was installed through the formation which would act as the internal overflow pipe.
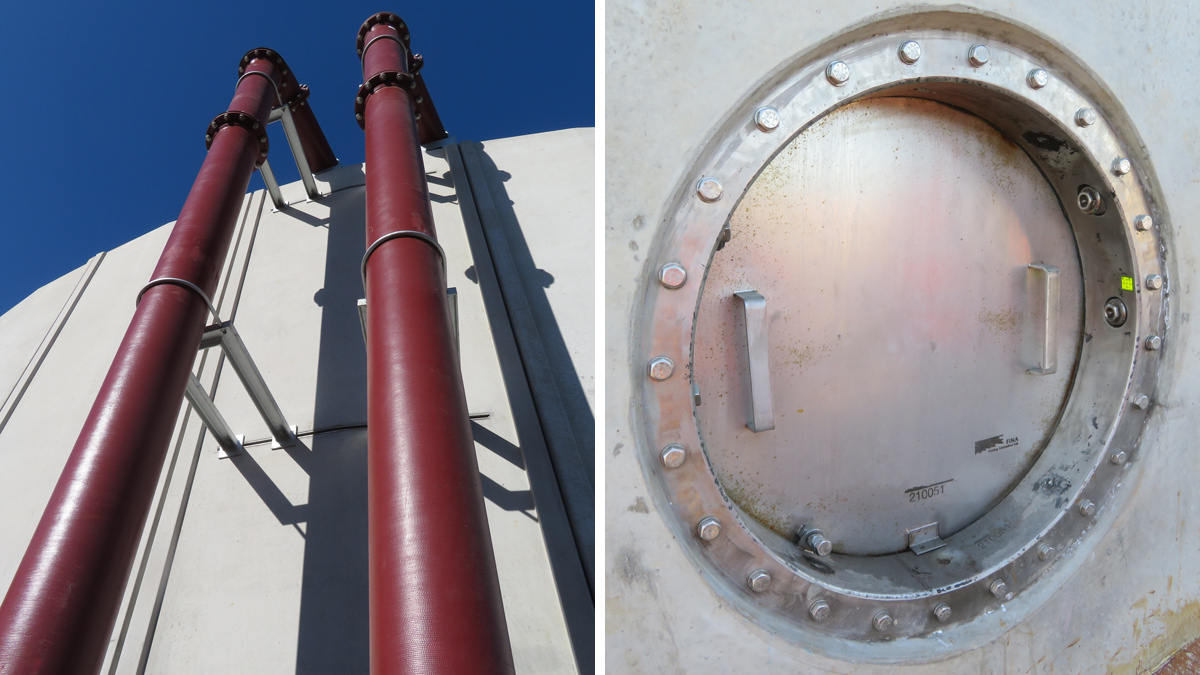
(left) Halfen channel cast into the panel during factory manufacture for easy installation of brackets/pipework and (right) bespoke stainless steel manway – Courtesy of A-Consult Ltd
Base plate design
In the early stages of the design, A-Consult Ltd needed to rethink and design a unique base plate for the 29m diameter storm detention tank at Horwich WwTW. The tank required a cleaning system and a highly detailed tank model was made using building information modeling (BIM), which coordinated the design, improved communication, and help avoid clashes with the project partners.
In addition, the top of the base, sump bottom and structure bottom were designed with a level of angle and the specific area to achieve easy handling and maintenance.
Design process of the precast concrete tank
In accordance with BS EN 1992 ‘Design of Concrete Structures for Retaining Aqueous Liquids’, the AQUA-TANK®-system was designed using pre-tensioned precast concrete panels with the exact dimensions, angles, and tensioning force to meet the high demands at the treatment plant. With over 8.500 precast concrete tanks designed and installed across Europe, the vast experience and knowledge within the design department of A-Consult Ltd ensured both a robust construction and optimised design process. The storm detention tank was designed with precast concrete panels prepared to facilitate pipework entry, mixer entry points, man-way access, external platforms and ladders which can be attached and supported by the panels.
A storm detention tank structure such as this is designed for extreme load situations – from post tensioning of horizontal tendons in an empty situation and from the water pressure of containing almost 5,000m3 of water introduced in a short time. The extremely durable AQUA-TANK® is constructed using compressed EPDM in the vertical joints between the precast wall panels to ensure long term robustness and tightness. Vertical pre-stressing of the panels during manufacture and horizontal post tensioning is introduced during installation to the wall structure to reduce risk of corrosion to reinforcement at any load condition. This combined design requires minimal maintenance and the system has a life expectancy previously only achieved with cast in situ installations.
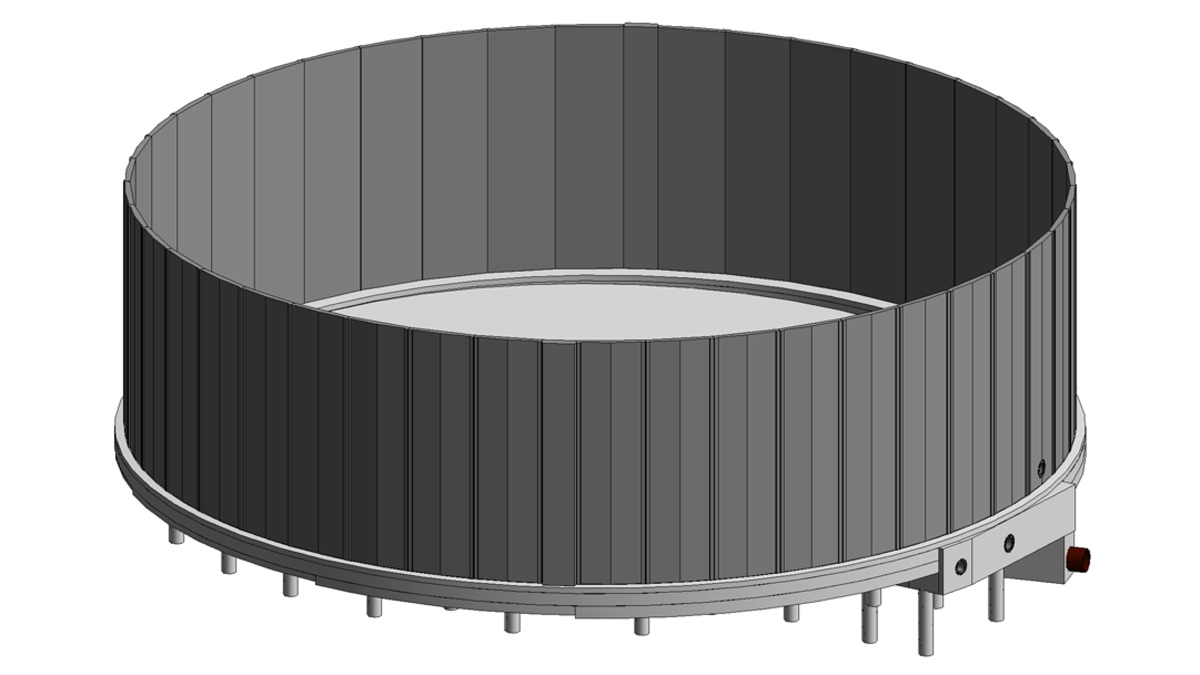
3D model of the Horwich WwTW storm tank – Courtesy of A-Consult Ltd
Tank construction
A-Consult Ltd used their own installation team to construct the reinforced concrete base. The base consisted of an external ring beam based on a stepped formation level with a consistent top level on which would have the pre-cast panels installed, and an internal base slab cast on a 1:100 fall with a 1.5m deep sump. Other adjacent structures also needed to be constructed during the tank build. Advance-plus used 4D planning software to review the programme with a focus on activity interface and the serviceability of the works, particularly the consideration of tandem lifting to install the precast panels. The use of this software identified an opportunity to complete the CFA piling to the adjacent Biomag building base slab whilst the storm detention tank was curing.
Precast panel installation was completed using two mobile cranes to off-load and set the panels vertically, before the lead crane positioned the panels. Temporary push-pull props were installed to retain the panels in position. Once all panels were installed, A-Consult Ltd then completed a post-tensioning activity and cast a secondary ring-beam around the toe of the panels to complete the construction. Advance-plus then carried out the water test.
Further construction activities
Advance-plus completed the interconnecting pipework and additional infrastructure to tie the detention tank into the existing process. This included approximately 200m of buried pipework at average depth of 4m, construction of a pump station to return flows to the inlet works and installation of new pumps and riser pipes into an existing detention tank to accommodate increase flows.
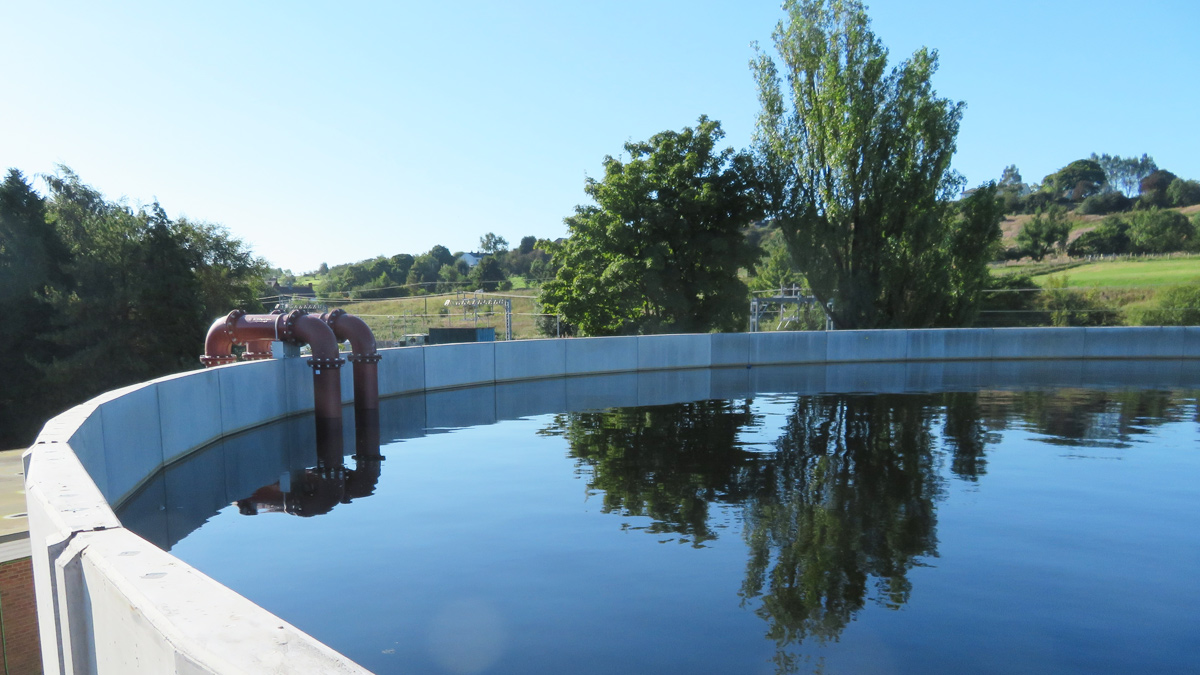
Horwich storm tank water test – Courtesy of A-Consult Ltd
Conclusion
The storm detention tank at Horwich highlights the flexibility of the AQUA-TANK®-system by A-Consult Ltd and demonstrates an ability to design and construct precast concrete tanks in close cooperation with business partners to achieve cost effective and optimized solutions across many applications within the water and wastewater sector. The robust, flexible and cost-effective design ensures numerous tank application possibilities within the water and wastewater sector including settlement, filter, process, storage, and storm detention tank systems.